Design Day Spring 2022
Design Day is an opportunity to share our Senior Design Showcase with the public. Seniors work in groups with faculty to design and test projects.
Senior Design Projects: Spring 2022
Our goal is to produce a non-intrusive sensor that will measure the relative flow rate of pneumatically conveyed coal particles through coal power plant piping.
Team: Hunter Bakos, Alex Maloy, Andrew Schager, Alex Shike (lead), Zachary Sturtevant
Faculty Advisor: Dr. Shad Roundy
Airbag inflator filters are asked to do several things in the inflator environment, including cooling of the pyrotechnic gases, filtering of particulates and some gas effluent control. Current methods for testing new filter designs require the building and testing of full airbag inflators which can be costly and also does not allow for efficient data capture. Our project focuses on designing and prototyping a testing device that can simulate the inflation process of an airbag and measure the temperature and pressure drop of the gases across the filter.
Team: Aaron Bruderer (lead), Landon Malo, Alex Query, ZiLong Wang
Faculty Advisor: Dr. Mathieu Francoeur
Design a dynamic tablet testing device for Autoliv that actuates at at least 1m/s and can measure force and position with a sensing rate of ≥100 kHz throughout collision with the tablet. The output data will be analyzed by Autoliv inflator development team and used to better model the mechanical behavior of the gas generant tablets during the ignition cycle of inflators.
Team: Nicholas Collins, Riley Lawrence, Hui Wang, Dallin Weatherford
Faculty Advisor: Dr. Pedro Huebner
This project aims to create a comparable alternative to aluminum circuit board housings using additive manufacturing and electrically conductive paint. When designing electronics, sensitive components need protection from noisy environments. Our group is testing this by running a series of experiments on conductive paints applied on different 3D printed substrate materials. These materials will be run through different environmental tests to assess how well the resistivity of the paints will hold up in conditions similar to what the aluminum housing would be subject to. Additionally, the 3D printed substrate needs to be comparable to the structural properties of aluminum. We will be analyzing this by performing numerous finite element analyses on each of the different substrate materials.
Team: Matt Barkey, Daniel Desaulniers, Jaden Fry, Sammon Hadjnorouzi, Lucas Foreman (lead), Max Wasilewski
Faculty Advisor: Dr. Pedro Huebner
L3Harris is looking for a solution to their electronics shipping needs that will replace the use of pelican cases which take up too much storage space when not in use, and cannot be adapted to multiple sizes of products. This solution must be adaptable and space efficient, while also protecting the electronics from shock, vibration, and harsh environments. Our design uses a set of eight 3D printed corner bumpers to provide protection while saving space and offering flexibility.
Team: Luke Bradley, Luc Rochat, Dawson Slaughter, Ethan Teachman (lead)
Faculty Advisor: Dr. Kam Leang
Automation of digital image correlation system including a vibration isolator to reduce effects from outside noise.
Team: Hayden Brooks, Jesse England, Kent Lancaster, Alex Larm, Akshil Patel (lead)
Faculty Advisor: Dr. Owen Kingstedt
Project Sponsor: Northrop Grumman
In order to improve safety and efficiency of the electrorefining process at Rio Tinto, a new design for a liberator cell hood is required that covers each cell individually and allows for easy cleaning of bluestone buildup between cells. These changes will both improve the safety of the cleaning process for the operator as well as increase efficiency of the electrorefining process by reducing deficiencies caused by bluestone created shorts in the electrorefining process. This project will entail remodeling the cell hood as well as implementing a new system for removing the cell hoods for cleaning.
The new cell hood is smaller, so it covers only a single cell, and leaves electrical contacts exposed for cleaning. The new design uses a y-connector to connect each pair of hoods to the same outlet pipe used by the current hoods. The new hood has four eyelets at each corner to connect to a lifting bale. The lifting bale can connect to an overhead crane at two points to improve stability.Team: Alex Coulson, Jake Ericson, Chase Gesteland, Ben Hamilton (lead), Eli Stephensen
Faculty Advisor: Dr. Sanford Meek
The overall goal of this project is to miniaturize MOOG’s Ella medical infusion pump. The Ella pump has two Hall effect sensors that measure dilation of the pump’s tubing in the case of occlusions or impedances to fluid flow, but these sensors take up significant space within the pump. Our approach to miniaturizing this pump is to use motor feedback to detect occlusions and impedances through monitoring the amount of current the motor is pulling. When the tube is blocked, the motor will pull more current and our motor controller should be able to detect that change and stop the motor before any damage can be done to the pump or the patient.
Team: Lauren Kochaver, Cole Paradis, Nikita Rabbitt, Sam Schmiett
Faculty Advisor: Dr. Mark Fehlberg, Dr. Ryan Stanfield
We will create a human powered vehicle utilizing a hydraulic and mechatronic system to compete in the NFPA Fluid Power Vehicle Challenge and win the Efficiency and Endurance Challenge.
Team: Dmitry Baxter, Tyler Boulter, Siddhant Devaru (lead), Barrett Kilroy, Jonathan Nuttall, George Timpson
Faculty Advisor: Dr. Meredith Metzger
Poster
As part of national competition, the goal of this project is to design an additively manufactured heat sink for cooling an electronic computer chip under forced air convection (an airflow velocity of 3.5 m/s). The heat sink must be designed using aluminum 357 and must have an optimal topology with respect to feature arrangement, size, shape, and location to maximize heat dissipation with minimal volume. Heat enters the system through two asymmetrical heat sources, requiring unique design to successfully dissipate heat.
Team: Aria Burk, Mateo Ismodes, Joe Lauer (lead), Spencer Nielsen, Chandler Schoenfeld
Faculty Advisor: Dr. Sameer Rao
Our project is to build Utah Student Robotics a test bed that allows them to analyze the performance of various lunar drum digger designs. The test bed provides analysis of X-Y force and torque measurements on the drum during operation as well as measuring the relationship between depth and force. In addition to these analyses, the drum digger can be removed so that different designs can be tested and compared.
Team: Stefen Gill (lead), Kenzie Hoggan, Charles Lambert, Justin Lord, Emma Stillings, Vivian Su
Faculty Advisor: Dr. Mark Minor
Traditional backpacking hammocks are limited in their use by their dependence on needing at least two anchor points to be lifted off the ground and held securely while in use. This limits backpackers who use hammocks to a small set of campsites that have properly spaced trees, or forces them to carry around a large heavy frame to support the hammock when two anchor points are not available. The objective of this project is to design and create a single point hammock system that allows a traditional two-point hammock to be anchored to a single anchor (such as a tree) instead of needing two properly spaced anchor points.
Team: Michael Auffenberg, Cole Laulis, Alec Martin (lead), Connor Phelps, Finn Navidomskis, Aaron Tang
Advisor: Dr. Ken Monson
When performing eye exams on outreach programs, ophthalmologists are away from their office full of helpful equipment and must rely on a steady hand and a still patient to obtain accurate results. This is not overly difficult for the first few exams but after performing dozens of exams over long periods of time, the quality of the exam suffers due to fatigue. Our goal is to create a headrest that ophthalmologists can utilize to increase the quality of eye exams performed under non-ideal conditions by holding both the patient’s head and the handheld slit-lamp used to perform the exam steady while maintaining a portable design that is easily transportable.
Team: Thania Arellano, Austin Davis, Collin Grant, Calvin Ho (lead), Jared Solosko
Advisor: Dr. Kenneth d’Entremont
Every year, there are unfortunate accidents involving residential riding lawn mowers riding over people or pets. In order to reduce the frequency of accidents, this project aims to install a series of sensors and a backup camera onto a riding lawn mower. Once integrated with a display in front of the lawn mower operator, he/she can have greater situational awareness resulting in lower rates of accidents. A bumper system mounted to the rear of the lawn mower will allow for a shut-off switch to be installed should the mower strike someone while moving in reverse.
Team: Riley Armbruster (lead), Robert Prescaro, Kaleb Runyon, Spencer Shull
Advisor: Dr. Ken d’Entremont
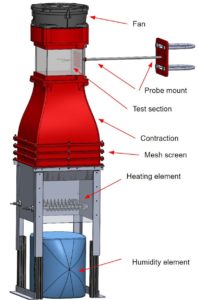
This project is to improve the current clinical neck traction procedure by introducing a mechatronic device to replace free weights, ropes, and pulleys. The neck traction mechanism was developed with guidance from an ergonomics expert and input from both neuro- and orthopedic surgeons. Communication between the involved parties has resulted in a design plan that includes several benefits over previous neck traction methods. The neck traction device is electronically controlled, provides real time input and output feedback via digital display, and is also adjustable with three degrees of freedom: extension/retraction, flexion mobility, lateral flexion mobility.
Team: Andrew Adams, Sterling Averett, Jee Ha, Simon Kahle, Derek Mitchell (lead), Seth Polevoi
Advisor: Dr. Andrew Merryweather
The objective of this project is to design and prototype a vehicle roof rack mounted lifting system that can move a user from a wheelchair to a handcycle and vice versa.
Team: Johnny Carlson, Evan Cleveland, Vito Kuang, Rian Simpson, Alex Wang, Niels Wheelwright (lead)
Advisor: Dr. Andrew Merryweather
Manual wheelchair users slow and stop their wheelchairs using their hands. For many users this causes friction burns on their hands. Our brake will attach to a manual wheelchair and can be used to compress the tires directly to slow or stop the wheelchair. It is lightweight and does not impede the user’s daily function, yet will allow the user to easily access and control the engagement of the brake.
Team: Josh Coombs, Nick Johnson, Nick Oram, Shelley Osterhout (lead), Zev Sun, Noelle Tenney
Advisor: Dr. Andrew Merryweather
Our role is to work with the University of Utah FSAE club to design a powertrain for their electric vehicle competition in the 2022-2023 academic year. The FSAE team currently is using a single motor drivetrain, which does not have torque vectoring capabilities which can increase speed. We will increase the performance of the drivetrain through the use of two electric motors with their associated controllers and necessary program logic. We are to work within competition rules, optimize vehicle performance for scoring events, and develop an efficiently running powertrain. We will need to operate within the team budget, working with current club members and advisors to ensure a reliable, fast, and efficient power system.
Team: Jon Chua, Will Graham (lead), Jeff Gubler, Luke McDivitt, Karianne Moe, Zach Orton, Dan Strum
Advisor: Dr. Ken d’Entremont, Dr. Sam Drake
Redesign of central hub and valves used in aerobic fitness testing to increase flow efficiency and user comfort during test.
Team: Jess Anstee, Parmit Chalise, Sarah Roberts (lead), Libbie Sudweeks, Cameron Williams
Faculty Advisor: Dr. Marc Calaf
We are working to reduce the weight and optimize the function of a telemark ski boot for backcountry and skimo racking applications.
Team: Ryan Beyer, Andrew Snyder, Jackson Willen (lead)
Advisor: Dr. Marc Calaf
In the United States alone, data centers use between three and five million gallons of water per day and require over 100 megawatts of power. Around 43% of that power contributes to cooling systems. Reducing both the water and power consumption of data centers is critical to keep up with public and private demand for data centers. To accomplish this, a passively-adjusting heat exchanger will be designed that relies on refrigerant changing phase inside a closed system to cool servers instead of the standard Computer Room Air Conditioner (CRAC) and cooling towers that are currently used.
Team: PJ Dowling, Kenny Ho, Thomas Jimenez, Jeff Perry, Samantha Simonich (lead), Peter Timmerick
Advisor: Dr. Kent Udell
The goal of this project is to redesign the thermo-fluid energy system for a new vacuum cold trap used in the distillation of natural oils. The current design is sub-optimal leading to long processing times and equipment failure due to uncaptured vaporized oil. Proposed improvements include increased vapor condensation to reduce pump failures, internal sensing for early fault detection, improved manufacturability, reduced assembly and cleaning time, and reduced cycle time.
Team: Ben Andrus, Jordan Lewis, Levi Marland (lead), Landon Myers
Advisor: Dr. Jacob Hochhalter
Sponsor: Soma Oil
Smart Trainer aims to assist physical therapy (PT) patients, gym goers, and athletes in performing exercises and minimize common injuries that arise from incorrect exercise form. By developing a reliable, safe, and inexpensive devices coupled with a mobile application that utilizes computer vision and sensors to give real-time haptic feedback. This will allow people to not only perform workouts safely, but also exercise from the comfort of their own home without the need for assistance.
Team: Tyler Bartunek, Ja-Rey Corcuera, Benjamin Hugo (lead), Gonzalo Tello
Advisor: Dr. Haohan Zhang
The goal is to create a single therapy, low cost, chemotherapy infusion pump. These pumps will be more affordable to anyone with cancer who qualify for ambulatory treatment.
Team: Joe Hudspeth, Mina Matta, Hannah Gracie O’Neill (lead), Jacob Scutt
Advisor: Dr. Mark Fehlberg