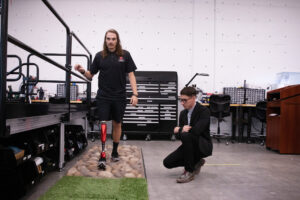
Researchers at the University of Utah’s Bionic Engineering Lab have developed the “Utah Bionic Leg,” the most advanced bionic leg ever created. Now, the university has forged a new partnership with the worldwide leader in the prosthetics industry, Ottobock, to license the technology behind the Utah Bionic Leg and bring it to individuals with lower-limb amputations.
“The largest prosthetics manufacturer in the world has committed to use the highest level of technologies available in robotics and AI to bring this prosthetic leg to those who need it as soon as possible,” said University of Utah mechanical engineering associate professor Tommaso Lenzi, who is the lead researcher on the Utah Bionic Leg project. “Ottobock promotes freedom of movement, quality for life, and independence. They are saying now is the time to make such technical solutions available to everyone.”
A ceremony and press conference announcing the partnership were held Wednesday, Oct. 5, in Lenzi’s Bionic Engineering Lab in the Rio Tinto Kennecott Building on the University of Utah campus.
Attending the ribbon-cutting ceremony were Professor Hans Georg Näder, owner and Chairman of the Board of Directors of Ottobock; Georgia Näder, Ottobock Supervisory Board Member; College of Engineering Dean Richard B. Brown; and Lenzi. Alec McMorris, an above-knee amputee who has spent years working with the lab, demonstrated the functions of the leg.
Utah Bionic Leg
Lenzi’s Utah Bionic Leg uses motors, processors, and advanced artificial intelligence that all work together to give amputees more power to walk, stand-up, sit-down, and ascend and descend stairs and ramps. The extra power from the prosthesis makes these activities easier and less stressful for amputees, who normally need to over-use their upper body and intact leg to compensate for the lack of assistance from their prescribed prosthetics. The Utah Bionic Leg will help people with amputations, particularly elderly individuals, to walk much longer and attain new levels of mobility.
“If you walk faster, it will walk faster for you and give you more energy. Or it adapts automatically to the height of the steps in a staircase. Or it can help you cross over obstacles,” Lenzi says.
The Utah Bionic Leg uses custom-designed force and torque sensors as well as accelerometers and gyroscopes to help determine the leg’s position in space. Those sensors are connected to a computer processor that translates the sensor inputs into movements of the prosthetic joints. Based on that real-time data, the leg provides power to the motors in the joints to assist in walking, standing up, walking up and down stairs, or maneuvering around obstacles. The leg’s “smart transmission system” connects the electrical motors to the robotic joints of the prosthetic. This optimized system automatically adapts the joint behaviors for each activity, like shifting gears on a bike.
Finally, in addition to the robotic knee joint and robotic ankle joint, the Utah Bionic Leg has a robotic toe joint to provide more stability and comfort while walking. The sensors, processors, motors, transmission system, and robotic joints enable users to control the prosthetic intuitively and continuously, as if it was an intact biological leg.
Just as important, the leg is designed to be extremely lightweight. It weighs about six pounds, which is half the weight of the next-lightest bionic leg. Heavy prosthetics are harder for amputees to walk on because they require more energy from the user and because it is harder to keep the prosthesis attached to the user’s residual limb.
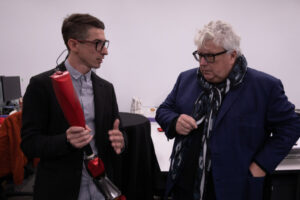
The Utah Bionic Leg’s advanced controllers, fine-tuned machinery, lightweight components, and patient-centered design has the potential to make life better for many above-knee amputees, particularly elderly amputees and those who lost a lower limb to vascular disease.
“As a health-tech champion, Ottobock always seeks to improve functionality and safety for patients and users worldwide,” says Näder. “Professor Lenzi’s technology promises to achieve exactly that. It is a superior prosthetic knee, incomparable to any currently available product. Our partnership with the Bionic Engineering Lab enables this innovation and offers great opportunities to unite Ottobock’s experience and knowledge with technologically exciting new possibilities.”
Ottobock Sponsorship
Ottobock’s sponsorship of the Bionic Engineering Lab will fund a state-of-the-art motion analysis system that includes a force-sensing treadmill and force-sensing staircase, 3D motion-capture cameras, and other equipment to help analyze how the Utah Bionic Leg benefits users and to discover new ways to improve their technology.
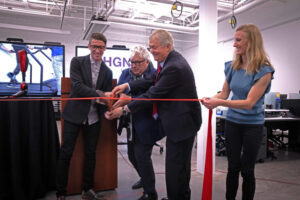
In exchange, Lenzi’s Bionic Engineering Lab will officially be called the Hans Georg Näder Laboratory, or HGN Lab. Ottobock will also gain joint ownership with the University of Utah for future technologies produced in the lab.
“This sponsorship will make the HGN Lab one of the best — if not the best — equipped lab in the world that is focused on assistive technologies and prosthetics,” Lenzi said. “And we have a development agreement where engineers in my lab and from Ottobock’s research-and-development division will work together to go from the current prototype of the Utah Bionic Leg and create a leg that will hopefully go on the market soon.”
Lenzi said this new partnership with Ottobock also ensures that his team can work effectively with Ottobock researchers by sharing each other’s expertise.
“We want to make sure the good ideas go from the lab to the market at soon as possible,” he said. “What we’re trying to create here is a partnership that will enable us to work together on these kinds of problems by combining the best of academia with the best of industry.”
Click below to see a demonstration of the Utah Bionic Leg.