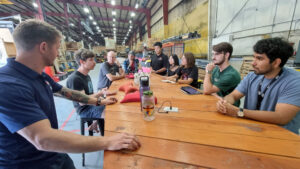
Top ranked speed climbers may only be hundredths of a second apart in finish times. As the U.S. Olympic Training Team looks for ways to take their best speed climbers from their current high world ranking to podium positions in Paris this summer and LA in 2028, new technology could be the key to improving training. With the proposed U.S. Olympic Climbing training facility to be built in Salt Lake City, Utah and the 2034 Olympics slated to be in Utah, the University of Utah and its students are a great fit for building that technology.
This opportunity began when Andrew Gill, the Capstone Coordinator for the Department of Mechanical Engineering, began a conversation Behan Abtahi from the United States Olympic Training Team about the Capstone program in the ME department at the U. Abtahi had previous experience working with the New Zealand Olympic team and their partnerships with capstone programs locally. Based on the success, Abtahi worked with Gill to bring the University of Utah Capstone program into the U.S. Olympic Committee Partner Alliance.
“I am excited for students to work on these projects,” said Gill. “Not only are they interesting real world engineering challenges, but they also generate a lot of excitement for the students because they will be used by top caliber Olympic athletes in training.”
Preliminary analysis from the USOPC Sport Performance Team determined that start mechanics, not reaction times, had the most impact on climb times, making it the focus for training improvements. With that knowledge in hand, the Capstone team was tasked with creating instrumentation to track multiaxial force data for the lower seven holds on two speed climbing walls. The device also needed to be interior to the wall and non-invasive in design to avoid interfering with training.
The team of students: Daisy Quach, Tren Hirschi, Lingbai Ren, Clarissa Seebohm, Gannon Brady, and Julian Torres worked with their advisor Dr. Stephen Mascaro to develop two different methods of collecting the necessary data. First, an Instrumented bolt, which uses four strain gauges on a machined 3/8” bolt. The strain gauge wires are routed through the hollow center of the bolt and a behind the wall a pin connector allows the strain gauges to be easily connected to an amplification/data collection circuit. The recorded strains are then calibrated into three-axis force data. The behind-the-wall design uses a commercial force transducer to collect the data. An internal plate is set within the hand hold and used to connect to another plate mounted to the transducer.
Both systems showed success as proof-of-concept. The data collected from the behind-the-wall system is nearly accurate enough to be used in training. However, this version is complex to install and not applicable to commercial gyms. The instrumented bolt offers a more deployable package; however, the calibration methods aren’t consistent enough yet for training purposes.
“Going forward, we would like to refine these ideas into a final design that meets the Olympic Committees accuracy targets,” said Gill. “The current plan is for a new group of students to carry on the project starting in Fall 2024. Their focus will be analyzing the contributing factors to the accuracy issues such as wall friction and load sharing between attachment points, as well as looking for other solutions that could reduce the force measurement inaccuracies.”
In addition to finishing this project, the ME Capstone program will continue looking for other opportunities to collaborate with the U.S. Olympic Committee Partner Alliance. The Capstone program regularly partners senior undergraduate mechanical engineering students with industry projects and helps bring them to life.
You can find out more about the ME Capstone program in the Capstone section of our website.