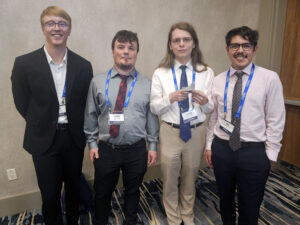
For the second year in a row a team of undergraduate students from the Department of Mechanical Engineering at the University of Utah have won the ASME/K-16 and IEEE/EPS Student Design Challenge. This yearly competition gives students the opportunity to design an additively manufactured heat sink. This year, the challenge required the heat sink to be designed under forced air conditions using stainless steel and operating under a lower power input.
This year’s team included Zane Frey, Eric Montenegro, Nathan Brown, Joshua Brodbeck, and Oliver Proctor, with Dr. Sameer Rao advising. In Fall 2023, the team began digging into the parameters provided to understand how they would affect the design.
“Stainless steel has a relatively low thermal conductivity when compared to conventional heat sink materials like aluminum or copper,” said Frey. “We knew that this, combined with the low power input of 3W, would significantly limit the usable design space.”
With that knowledge, the team decided to perform a parametric study to investigate conventional plate fin heat sink designs to act as a benchmark to compare their new designs against. By varying the number of plates, plate thickness, and plate height, they identified the optimal heat sink based on a figure of merit (FOM) comparing thermal performance to the heat sink’s mass.

“We experimented with more creative designs that pushed the limits of additive manufacturing,” said Frey, “but those early designs didn’t outperform the benchmark plate fin heat sink. This led us to work on a design that tailored to this year’s challenges and built on the conventional plate fin heat sink design.”
The low thermal conductivity proved to be the major hurdle to overcome with any design. As the team evaluated the physical phenomena involved, they found that they would need to increase convection heat transfer near the base plate to facilitate localized cooling. This led them to the geometry of a venturi tube, where the roof would create a channeling effect of airflow through the heat sink by capturing as much air intake as possible. They also explored various methods to reduce mass while maintaining thermal performance.
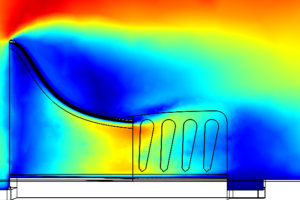
The team submitted their final design and were selected as semifinalists, allowing their design to be printed using GE’s binder jet technology for experimental testing. They also had the opportunity to present their design at ITherm 2024, where they were chosen as the winners of the competition.
“Our team is thrilled to have won the competition. We invested countless hours into the project and seeing it pay off makes it all worthwhile,” said Frey. “Watching our project evolve from concept to physical prototype and presenting at ITherm 2024 was an incredible experience. Special thanks to Dr. Sameer Rao for his guidance and to Alik Nielsen for his help with physical prototyping at the U’s 3D Metal Printing Lab.”
In addition to the win last year, the U’s undergraduate team also won the competition in 2020 and will continue to compete moving forward as part of the senior design capstone program.