The 2021 ASME/K16 and IEEE/EPS Heat Sink Design Challenge was an international competition where students competed to design an additively manufactured aluminum natural convection heat sink that provided maximum performance. The heat sink had to be designed to operate at as low a temperature as possible for as low a cost as possible. It also needed to be designed to leverage the new possibilities created by additive manufacturing (metal 3D printing). This year’s winners were a team of University of Utah students from a total of 22 participant teams.
“Since its inception in 2018, the ASME Heat Sink Design Contest has explored the intersection of additive manufacturing and practical thermal design,” says Dr. Rao. Dr. Rao has been a part of the organizational committee since 2019.
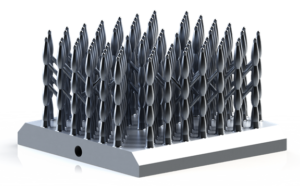
As part of this design challenge students are tasked to design, build, and validate an aluminum heat sink made with Additive Manufacturing techniques made available to the teams by GE Additive. After learning about the year’s scoring criteria and manufacturing constraints, the students must prepare a white paper that justifies their design. This can be done with preliminary CFD/FEA modelling, empirical correlations, etc. The top white papers (reviewed and ranked by industry and academic experts) are selected to have their parts printed with GE Additive machines. Those heat sinks are then be sent for testing to determine the top designs. From the top teams, one member can travel to ITHERM where they will defend their design in front of industry leaders. The champion is crowned at the IEEE ITHERM conference based on oral presentations and the performance of the printed heat sink.
This year’s U team consisted of Travis Allen, Michael Alverson, Carter Cocke, Bence Csontos, Hunter Scott, and Erik Steenburgh, with Dr. Keunhan Park and Dr. Sameer Rao advising. The team dove into research during their senior design course in Fall 2020, doing as much background research in fluid mechanics and heat transfer as possible to prepare them for the competition.
“The 2021 competition involved designing a forced convection heat sink,” said Csontos, “so after our initial research phase we began designing a forced convection heat sink to practice what we learned from research papers. We also toured a local additive manufacturing company to get a sense for the limitations of additive manufacturing to consider in our design process.”
Because the 2021 guidelines involved designing a natural (free) convection heat sink instead of a forced convection heat sink, the team had to pivot and catch up on the latest research in that area. The team used tools including finite element analysis (FEA) and computational fluid dynamics (CFD) to design, test, and quantity the performance of different heat sink designs.
“We arrived at a pin fin shaped heat sink that had a series of revolved airfoils stack on top of one another to maximize surface area, minimize mass which reduced cost, and utilized principles in fluid mechanics and heat transfer physics,” said Csontos.
This design used natural convection heat transfer physics, a process where air rises from a heat source due to density gradients in the air. Hot air rises because it is less dense than the ambient air surrounding the heat sink, so the fins on a heat sink dissipate heat from the heat source. As semi-finalists, the Utah team was also invited to participate in an additive manufacturing workshop organized by GE Additive. This was a tremendous learning experience for the students as they learned the tips and tricks that are necessary to realize practical and printable geometries from their conceptual design.
The team’s design featured the highest figure of merit (FOM) in both simulations and experimental testing at Oregon State University. They also put together a strong white paper and presentation that helped them win the competition.
“The competition was a lot of fun,” said Csontos.
On behalf of the team, we graciously thank the organizers and sponsors (GE Additive, COMSOL).