Design Day - Fall 2018
Design Day is an opportunity to share our Senior Design Showcase with the public. Seniors work in groups with faculty to design and test projects.
Additionally, freshman and junior mechatronics’ students compete and showcase their skills.
Senior Design Projects
Development of new biologic therapies can cost, on average, $2.6 billion, can take 10 years for development, and many do not even make it through clinical trials to market. Carterra hopes to significantly reduce cost and time while increasing success rates with a new testing procedure that would develop a database of effects between antibodies and antigens for pharmaceutical research. This procedure would make use of microfluidic technology developed at the University of Utah. Current technology can handle 96 samples at a single time; however, because the device can handle so many samples, the company and microfluids lab require a cost-effective pumping solution for their device. In addition to a low cost, the pump needs to produce flow rates between 5-200 µL/min with very little pressure noise.
Our group developed a novel solution we call the Constant Contact peristaltic Pump (or CCPP). The CCPP smashes medical tubing between rollers to produce flow. By innovating on current pumping solutions, we have made high volume microfluid pumping cheaper and more effective than similar products on the market today. (96 Channel Pump Array Poster)
Team: Joseph blash, Brian Lee, Joseph Blash, Connor Wade (lead)
Advisors: Dr. Bruce Gale, Brady Goenner
The PADS is a pontoon boat that functions as a mobile docking platform with wheel chair accessibility. It serves as a hub for multiple water activities for the TRAILS program, a comprehensive outreach program of the Rehabilitation Center at University of Utah Health© for individuals with spinal cord injury or disease. The PADS allow accessible controls that can be used by tetraplegic patients, physicians, and clinicians. This project gives the opportunity to patients with limited limb capability to be able to maneuver a watercraft.
Our team was tasked with creating an advanced navigation system for the PADS with controls for two modes of operation, open water and docking. The team designed and produced a Sip N’ Puff with an added bite piece for increased input parameters to control a four Degrees of Freedom system. A control scheme was created to control the mid-ship motor in tandem with the rear motor that will perform differently depending on the mode selected. A water-resistant control panel and motor control box were designed to safely house the electrical components required for this system. (Advanced Navigation Control for a PADS Poster)
Team: Nathen Blas, Brian Dorcheus, Colter Mckean, Cody Salyer (lead), Daniel Sant
Advisor: Dr. Andrew Merryweather
The American Veterinary Medical Association (AVMA) states that 30.4% (approximately 36.1 million) of American households own at least one cat. Cats are the primary known carriers of toxoplasmosis. Toxoplasmosis is a parasitic infection that presents a possible danger to pregnant individuals as it can be transferred to a fetus. If transferred during early stage development, serious and significant birth defects can occur, including impaired eyesight, seizures, and intellectual disabilities.
To avoid possible transfer of toxoplasmosis during pregnancy, it is encouraged to have non-pregnant individuals change cat’s litter regularly. This senior design project looks to improve current generation automated cat litter boxes. Improvements needed include decreased noise, automated refilling, reduction of waste order, easier waste disposal, and faster cycle times. The developed system is able to reliably self-clean (or sift) litter to remove waste, automatically refill the litter box with fresh litter, and is able to accommodate cats of all sizes, from kitten through adult. (Automated Litter Box Poster)
Advisor: Dr. Owen Kingstedt
One in six couples of reproductive age worldwide are affected by some form of infertility. Procedures to initiate pregnancy such as intrauterine insemination (IUI) and in vitro insemination (IVF) require several semen preparation steps. These current techniques are time consuming, expensive, may lose viable sperm, may cause damage to sperm, and involve human interaction steps that can lead to error. The collection of these problems drives a demand for a solution of a faster, simpler, and gentler technique that allows for a higher recovery of quality sperm.
The Microfluidics Lab at the University of Utah has developed a microfluidic chip that separates particulates in micro-channels which can be used for separating sperm from semen and can do so much faster than current techniques. The goal of this project is to develop a device that that will implement this new technology and automate the multi-step semen separation process, preparing semen samples for intrauterine insemination and in vitro fertilization. (Biomedical Device Development for Andology Clinics Poster)
Advisor: Dr. Bruce Gale
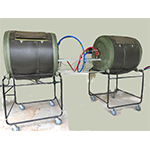
Team: Jacob Jarrell (lead), Aaron Kracke, Diego Piraquive, Regina Zambrano
Advisor: Dr. Marc Calaf
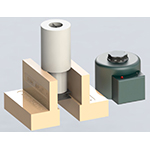
Team: Brandon Bungas, Shea Cullison, Youself Fahkroo,Michael Hartling, Jared Morales (lead)
Advisors: Dr. Shad Roundy, Robert Cheatham
Aerodynamics play a significant effect on vehicle dynamics, and good aerodynamic design is not restricted to creating a slippery car with a low coefficient of drag. Much like how wings are designed to lift an aircraft, aerodynamic devices like spoilers, splitters, and diffusers can be fitted to a vehicle to press it into the road, creating an effect known as downforce. The vehicle can turn more quickly as result, with the threshold of force its tires can withstand improved. The cost of downforce, however, is additional drag, which reduces the vehicle’s top speed in a straight line. A way to mitigate this cost is to add a mechanism which alters the geometry of the aerodynamic device while the vehicle is in motion, much like flaps on an airplane wing. This will allow the vehicle to have variable drag and downforce, which can be taken advantage of by minimizing drag during acceleration, while still obtaining the benefit of downforce during braking and cornering. Our senior design team has developed one of these active aerodynamics systems for the student built Formula SAE race car. (FSAE Active Aerodynamics Poster)
Advisor: Jon Davies
The miniature rockets project looks at the effect of two retropropulsion flows working against each other and creating a supersonic flow interaction. Supersonic retropropulsion is a promising solution for spacecrafts to decelerate in space, thus attracts many research attentions. Conventionally, this type of study requires expensive full-scale experiments that are out-of-reach for general university researchers. The objectives of this project require that the setup to be low cost and consists of only widely available materials. In addition to that, the setup features a digital sensing and data acquisition system to measure and collect real-time data during the experiment. The setup also provides clear visualization of the shock waves for at least 5s without the interruption of water vapor condensation, allowing clear video recording of the shock wave. Finally, parts with complex geometries (nozzle and wind tunnel) are manufactured with 3D printing processes, allowing quick and low-cost prototyping. (Miniature Rocket Poster)
Advisors: Dr. Kuan Chen, Donovan Chipman
The RASM’s primary function is to provide automated six degree-of-freedom pose control of a Tobii Screen. The Tobii screen is a device that uses eye-tracking software to help patients with spinal cord injury to operate a computer. The current systems to position the Tobii Screen are mechanically passive. This means when the patient’s head moves, they may lose the ability to comfortably control the screen because their eyes are no longer in position for the eye tracking software. They must wait for a caretaker to return before they can resume use. The purpose of the RASM is to solve this problem by using a robotic arm to automatically keep the Tobii screen directly in front of the patient’s face. (RASM Poster)
Advisor: Dr. Andrew Merryweather
ASHRAE 2018 Applied Engineering Challenge: Temporary Refugee Shelter – December 2015, for the first time ever according the the UN Refugee Agency, the number of forcibly displaced families surpassed 60 million. This has been a growing trend over the last two decades and the 2018 ASHRAE Applied Engineering Challenge presented students the opportunity to explore potential shelter solutions for the refugee crisis.
This international ASHRAE competition last spring consisted of a shelter design competition that included size restrictions, climate constraints, and ASHRAE standards as design considerations. The final design of a foldable shipping container was submitted to the ASHRAE Applied Engineering Challenge in June 2018; the submitted design placed 3rd overall.
This semester, the goal is to integrate renewable energy generation sources into the initial design for a wide range of climates and determine the practicality of this integration. Integrated renewable energy generation sources would allow the shelter to be self-sustained for off-grid applications and where power is not reliably accessible. (Temporary Refugee Shelter Poster)
Advisor: Dr. Amanda Smith
The ski industry is a highly competitive, rapidly evolving market where new designs and technologies are introduced every year. The biggest roadblock to innovation is the time and money it takes to prototype new ski designs. Our goal was to make an intuitive, easy to use ski press that features an adjustable camber system and digital temperature and press monitoring systems to allow for a wide range of flexibility in both the ski/snowboard geometry and accepted materials for rapid prototyping. (Snowsports Innovation and Design Poster)
Advisor: Dr. Michael CZABAJ
Research into the movement and burrowing of grubs and other similar pests is an ongoing effort that spans several different fields. These pests can attack gardens, fields, and other areas of agricultural operation. Live grub behavior is difficult to control in a lab setting, so studying grub movement becomes challenging. Our project examines the possibility of creating a soft robotic grub to streamline research in this area.
We have been tasked to design a robotic grub that is able to perform the same motions as a grub in a controlled and repeatable manner to be used in measuring strain in Dr. Fu’s test environment. We focused on three motions: Body bending to move inside the grub burrow, head motion to shovel dirt, and arm motion to push dirt freed by the head. Our team developed a method to cast silicone parts capable of mimicking grub sizes and movement, which are actuated using pressurized fluid. The soft robot is compatible with an ODROID microcontroller to allow a user to control each motion independently. (Soft Robotic Grub Poster)
Advisors: Drs. Henry Fu, Kam Leang
With the increasingly devastating effects of global climate change, renewable energy resources are becoming paramount in today’s world. Conventional horizontal axis wind turbines (HAWT) are less effective in gusty wind environments, which means much of the wind energy in places like Salt Lake City is not currently accessible. A quarter-scale vertical axis wind turbine (VAWT) was developed to show whether it is a viable device for harvesting wind energy in gusty urban environments. The wind turbine will also be used to publish a paper comparing theoretical, lab, and physical results in correlation with Dr. Meredith Metzger’s research. (Vertical Axis Wind Turbine Poster)
Advisors: Drs. Michael Czabaj, Meredith Metzger
The goal of this project is to produce a device that will enable patients with tetraplegia to fish with as much independence as possible. In order to grant this independence, the device is required to mount to the user’s wheelchair, cast out a baited line, reel it back in, and communicate with the user throughout the entire process. The casting system will be designed to provide the ability to change the direction and distance of each cast. The reeling system will be able to offer variable speed, providing the user with multiple fishing styles. The user interface will be compatible with all levels of disability and offer multiple feedback and control options. One example of a control method includes sip and puff technology, which does not require motor functionality of the limbs. The combination of these components is intended to optimize patient experience. (Tetra Fisher Poster)
Advisor: Dr. Andrew Merryweather
Laser cutting has become increasingly important in industry due to its ability to cut complex parts in short time. However, the technology suffers from two major quality effects, namely dross and striation. Dross and striation are the recast layer formed on the bottom side and along the cutting edge of the workpiece, respectively, after the cutting is done. In this project, we work on a novel process called Ultrasonic Vibration-assisted Laser Cutting Head (UVLCH), in which an ultrasonic vibration is applied to the laser during cutting to eliminate defects. The main goals for this project are to conceptualize, design, and prototype a vibration mechanism that enables the UVLCH, and conduct proof-of-concept experiments to demonstrate the future UVLCH. (Ultrasonic Vibration-assisted Laser Cutting Head Poster)
Team: Abdulrahman Asiri, Ben Brunty, Almahdi Mohsin (lead), Shafiq Rahim, Muhamin Ruslan
Advisor: Dr. Wenda Tan
The task assigned to this team was to create an Untethered Magnetic Haptic Interface to be used in the training of eye surgeons and student doctors. The primary goal of the interface is to allow medical students and surgeons to receive real-time force feedback while practicing eye surgery in virtual reality (VR). Giving them a realistic training experience before attempting the real thing on real patients. The system will use an array of electromagnets to create the force feedback provided to the user. A system using magnets like this differs from the use of lever arms and motors in traditional haptic devices, and is believed to create a more realistic user experience by eliminating mechanical inertia. Team EyeSee’s primary focus was to create a cooling system and non-ferromagnetic structural frame for the magnets, allowing them to receive the large amounts of current necessary to generate force feedback without overheating. (Untethered Magnetic Haptic Interface Poster)